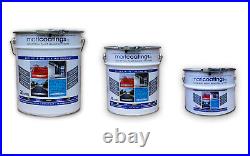
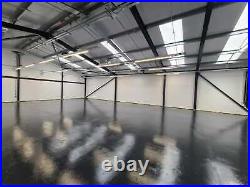
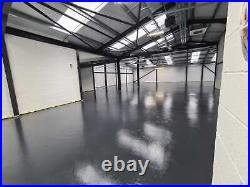
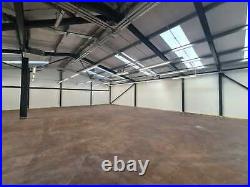
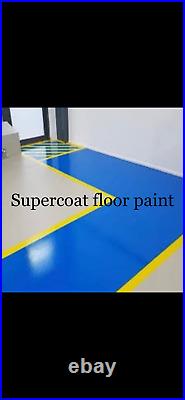
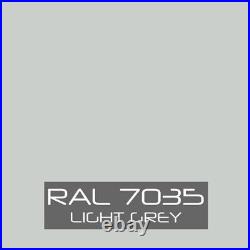
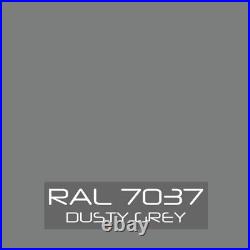
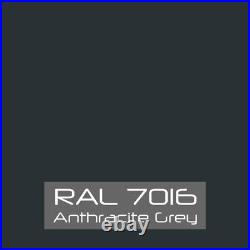
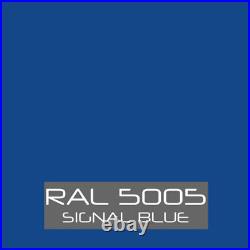
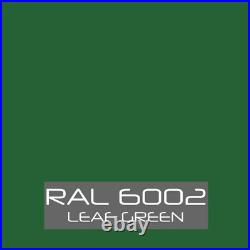
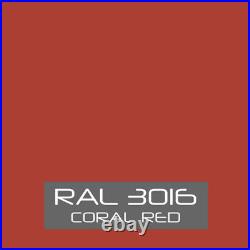
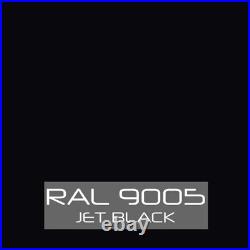

INDUSTRIAL SINGLE PACK FAST SET FLOOR PAINT. WE HAVE FORMULATED A SINGLE PACK ARRIVE AND APPLY COATING THAT GIVES THE APPLICATOR THE EASY OPTION WHEN APPLYING BUT WITH THE BEST RESULTS. Heavy duty industrial polyurethane high impact easy apply coatings for use on most floors including. This coating can not be used on Screed (powerfloat) smooth/shinny areas or bitumen type floors. To be suitable for use on factory floors industrial floor paints must generally be tough and resistant enough to withstand. The abrasion and wear that will take place i. From fork lifts, pallet trucks, cars, 4X4 plus other vehicle movements across the factory floor. The static loading that is imposed on the painted factory floor surface by pallet stacking in storage, or other equipment on the floor. Most liquid or chemical spillages that may occur on the floor i. Water, oils, Cutting Agents, Soft acid cleaning agents, wheel/brake cleaners, engine coolant, brake fluids some fuel’s etc that are used in the processes carried out on the painted floor. (do not leave these to sit on the area coated they must be removed and not left to soak into the area, they will with stand the spill but not for long periods of time). This is a user friendly coating that can be applied to a professional finish with even the most limited coating or application knowledge, it is a simple remove the lid mix the product to activate and apply with a roller or brush its that simple for the above results in the images. Most factory floors are reinforced concrete and this must obviously have sufficient strength to support all of these loadings and uses. The functions of the industrial floor paint are. To strengthen and improve the factory floor surface. To eliminate dust build up on surface (pre seal primer coating is always advised on dusty unpainted areas before a topcoat is applied). To increase the floors abrasion and wear resistance. To provide the increased additional chemical resistance. To control surface dust that is let off from uncoated concrete bases. To improve the appearance and ambience of the working environment. To speed up the cleaning/mopping of the area cutting down on time of this task and also to help combat dust issues on stock and surface contamination. To delineate specific areas, such as: safe walking areas, parking bays or access routes and other directions etc. This coating can be applied in domestic and industrial areas internal and also external the product is not water proof but will resist rain water when cured. For areas that are dusty and unstable, you will need a product that has been designed for maximum penetration while providing a good film build by re-bonding the substrate together, returning the floor to a solid sound surface the product we advise is our floor primer/underseal this can be found on the floor paint drop down menu. Oily / Contaminated Surfaces. Where the floors have been subjected to oil and grease, We recommend steam cleaning your floors and use a Heavy Duty Surface Deep Clean before application of any floor coating, after allowing the surface to dry and floor primer or other recommended primer has been applied a top coat can then be applied please do test patches on each stage of this process. A floor coating does not do well if you have any moisture issues Hydrostatic pressure from the moisture can actually cause the coating to peel up, sometimes taking pieces of the concrete with it. Should floors be devoid of an effective Damp Proof Membrane (DPM), virtually any paint will lift and peel off the surface. Indeed, even self-levelling screeds can be pushed up by water pressure. This is another nightmare regularly experienced by many companies. For this reason, a damp-proof coating is recommended as a solution before applying a floor paint. Treating your floor before coating them. It is important to treat your surfaces before coating them to prevent issues post-paint. Before painting your garage floor, it is important to repair any cracks, holes or expansions of joints in your concrete to prevent an un-slightly finish to your flooring once its painted. New laid areas of concrete should be left to cure for a minimum of 3 months before a floor coatings is applied then surface tests must be done before using this coating contact for free testing information. Product & Application information. Coverage:10m squared per litre or 107ft squared per litre. 200m squared per 2,100ft squared per 20litre tub (as listed). (Two Coats Always Advised). Dry time of coating using standard roller in areas with minimal air moisture (lab conditions). In winter months please allow extra time for curing, 5% white spirits can be added to the product in winter months to help with these sub 15’c temperatures and help combat slow drying times, when coating in these months please still open as many windows and doors possible to create a natural air flow over the coated area a space heater can also be added, do not trap warm air as this will also keep the coating soft as it is a polyurethane product. Do not apply over water, oil or grease any contamination will have to be dealt with before coating of that area get in contact for tips and advise via the message tab on this site. First coat should be left to dry for 24 hours to assure adhesion to surface leave minimum of 24 hours for after coats always leaving minimum of 48 hours before 100% use of area again. True 100% cure will only be 7 days after application of last coating. Applying multi thin coats is advised and not thick coats. (as thick coatings will surface dry and the under layer will remain soft). Work in a well ventilated area, using no forms of naked light/fire. Please test for damp before coating by applying a small test patch or applying a clear plastic sheet (30cmx30cm) and sealing it to the floor with a high grade tape (duck tape) with out any ways of air escaping and leave for 24 hours if there is any forms of water vapour on the sheet the are will have damp and steps will need to be taken before coatings. Mix very well before use using a drill/paddle tool. If the area you are looking to coat is virgin (never been coated) or has had contamination from oil, grease, cutting agents etc, Cleaning with correct equipment/surface preparation products will be required. Quick tip:on virgin surfaces or areas with adhesion issues with past coatings apply a small amount of water to the bare concrete if the water beads on the top the surface will need acid etching or abrading if the water soaks in then it will be fine to start steps towards coating. Powerfloated/Screed areas (smooth shinny concrete) will need to be treated with a acid etch or abrade by mecanical means all product info will be displayed on the item you will take collection of product safety data sheets can be requested on all our range. A test patch is always advised as some areas my still have contamination and this could have complications when coating. 24 HOUR DOOR TO DOOR TRACKING AS STANDARD WITH ALL OUR ITEMS. Or keep a note of batch code from lid of can. PRE-SEAL ITEM IS A UNDERCOAT/SURFACE SEAL AND SHOULD ALWAYS BE OVER COATED WITH A FLOOR PAINT PRODUCT THE PRE-SEAL PRODUCT ON ITS OWN WILL NOT ACT AS A STABLE FLOOR COATING. Floor-paint Products are polyurethane heavy duty high impact formulation and care should be taken when applied full safety data and coshh sheet can be requested. All images are for illustration purposes only and shade difference may happen from image to product. All of Isle of Wight, Isle of Man and Isle of Scilly and The Highlands and Islands and also the following area postcodes. DD, DG, EH, FK, KA, KW, KY, ML, TD, AB, PA, PH 95% of these postcodes are 3/4 day service. Any recommendations and advice offered are given without legal responsibility. To the extent permitted by applicable law. Shall not be liable to any person for any loss or damage which may arise from advice given or from the use of any of the information contained in any of the materials offered on this website. Not to be used on bitumen type floors always do a test patch prior to coating a whole area.
